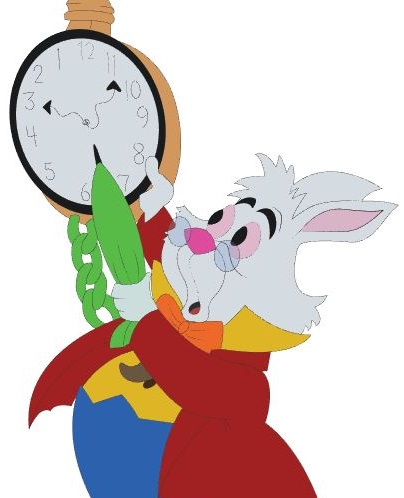
1534961683000
Time to market blog / Rapid Prototyping / Plasmotec
Getting the product into the market as quickly as possible is of paramount importance. Rapid prototyping can help this.
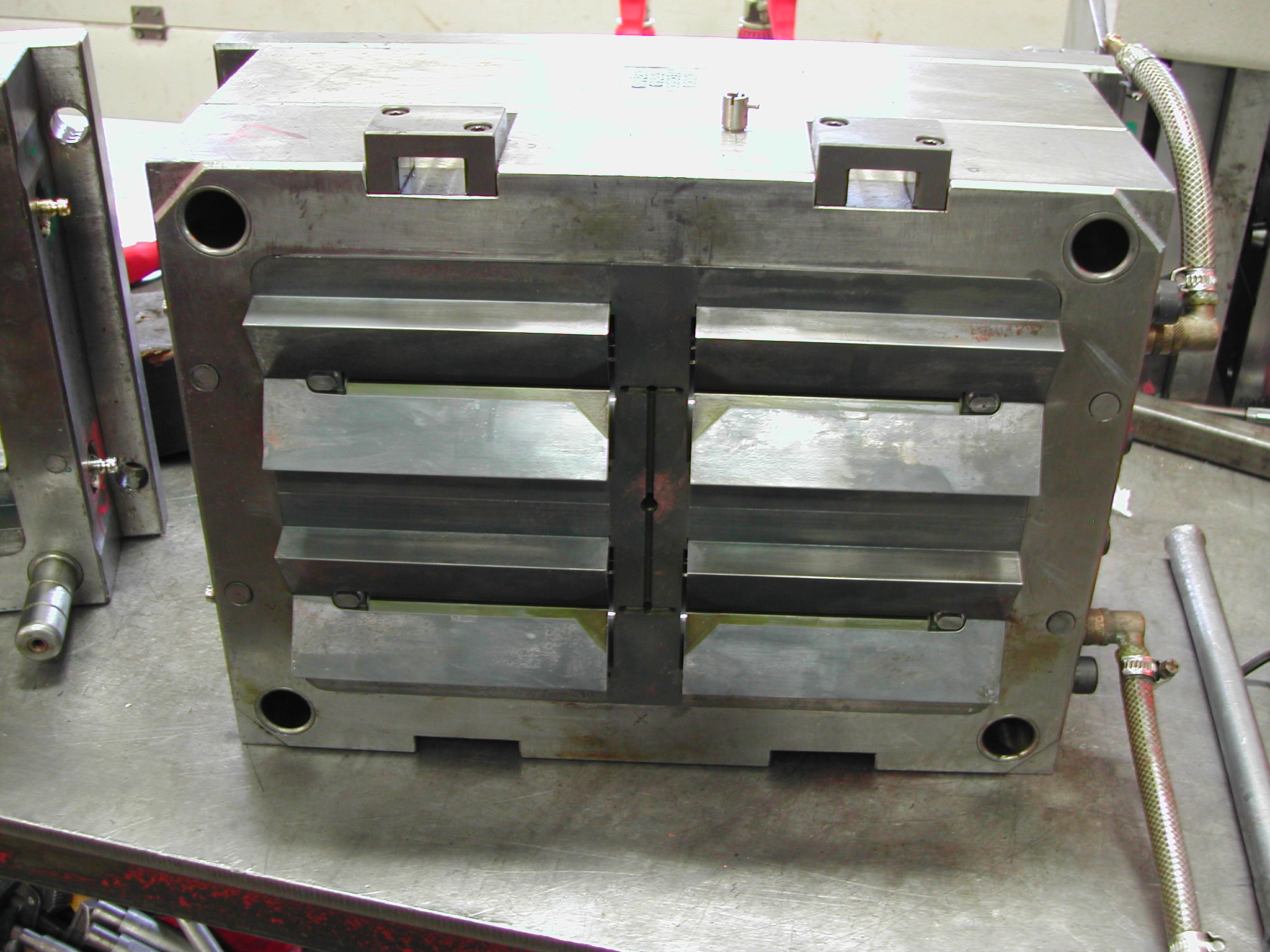
1523356255000
Orphan Tooling | Tool Re-homing | Transfer Tooling
Moving your tooling to a new supplier. Tool re-homing or outsourcing can be a worry, the question that haunts one is “am I jumping out of the frying pan and into the fire”. Plasmotec has a proven history of re-homing orphan tooling, be that single tools or complete suites. Our Toolroom and Production technicians are on hand to smooth the path to effective transfer, relieving you of the worry and headaches of the re-homing process. Most modern tooling is designed to fit to Euromap standard moulding machines, and therefore movement of the tooling to Plasmotec is simplified considerably. The Euromap standard means that there are usually only minor tweaks to be made to the tooling to allow it to fit to our portfolio of moulding machines. Any tooling work to allow the tooling to fit to our moulding machines can be completed free of charge in our on-site toolroom. There are a number of logistical issues to be borne in mind when looking to outsource or re-home your tooling, such as the time that it will take from the last off production by the incumbent moulder, to the point where the new moulder has everything buttoned up ready to produce your next order. This time frame will need to take into account the time that it will take to physically move the tooling from one moulder to the other. This can be quite extended if the tooling is currently homed abroad, you would need to be thinking of 6 – 8 weeks if the tooling is in China. Further the new moulder will need to receive and prepare the tooling to run on their machines, and dependent upon the number of tools to be moved, sufficient time allowance will need to be made to facilitate this work. Obviously, you will need to have component stocks in-hand sufficient to allow you to continue your business whilst the tooling is moved and the new moulder prepares the ground to continue supply. If you require a specific material, a bespoke colour or a special additive, you should ensure that the new moulder is informed of your specific requirements, and that they have this in-hand for your first order. At the appropriate time, you will need to inform the incumbent moulder of your decision to move the business, you will then need to move quickly to get the tooling prepared for shipment. If it is not physically possible for you to be present at the point that the tooling is prepared for despatch, you should ensure that sufficient photographic evidence is available such that the condition and completeness of the tooling can be accurately assessed and verified. The advantages of coming to Plasmotec are: Increased output levels from machines running 24 hours a day and a range of machines to choose from, therefore avoiding delays.Reduced lead-times and stock holding requirements if you are re-homing the tooling from China or similar.Utilising our on-site toolroom and our comprehensive tool maintenance programme.Improvements in consistency of product quality by having access to our optimisation and validation quality and manufacturing procedures.Cost effective tool upgrade options.Competitive unit prices for supply of your product.No set up fees. *No storage fees. *Nice helpful people to make the transition as pain free as possible. *Terms and conditions apply.​
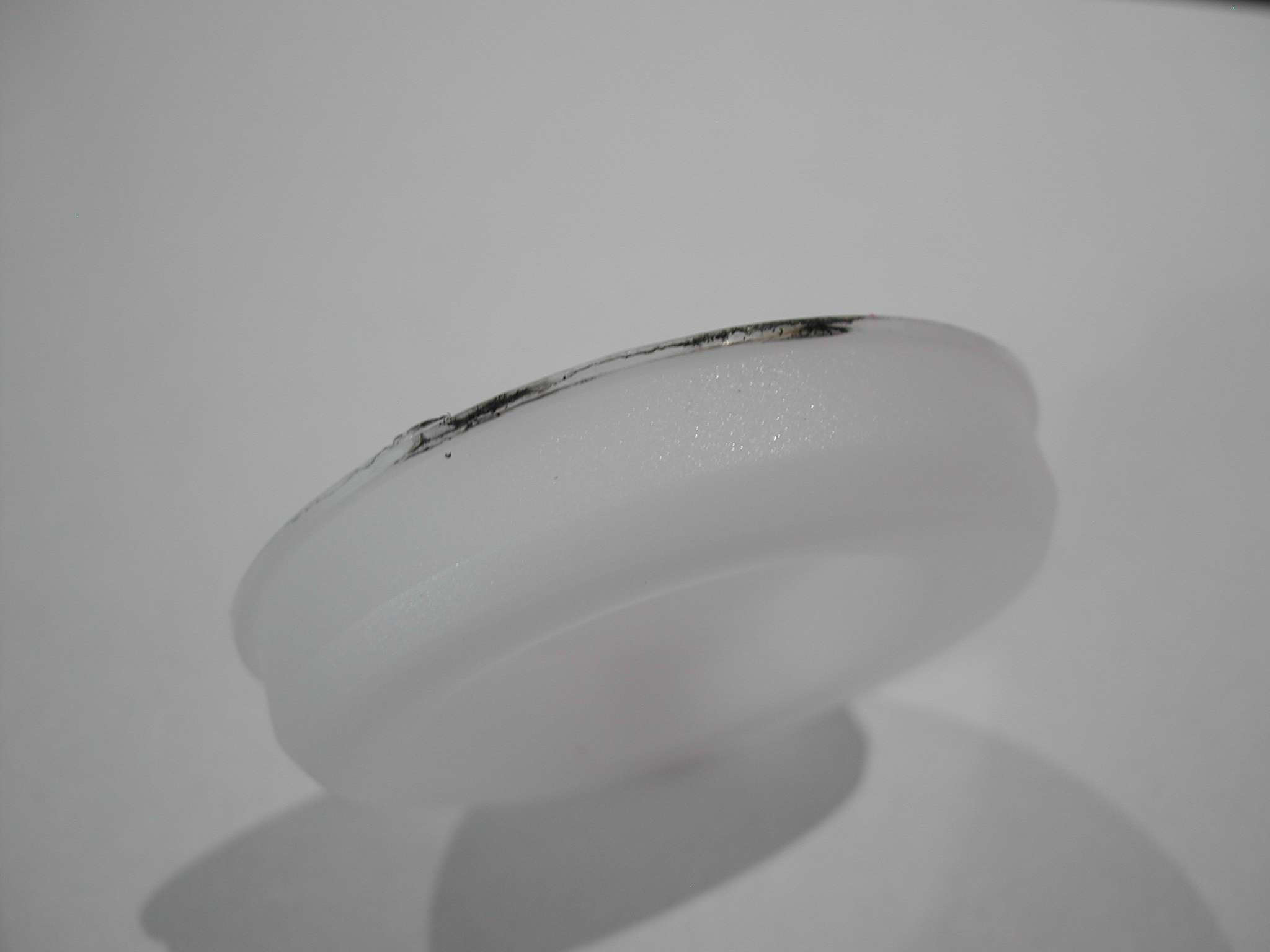
1522164549000
Injection moulding
When an injection moulding tool shuts during its normal cycle on the machine a volume of air is entrapped in the cavity, this volume of air is compressed as the hot melt plastic is injected into the tooling.

1520618272000
Plasmotec – The caring home for Orphan Tooling​
Give your tooling the care and attention it deserves and reap the benefits from happy well-adjusted tooling ! Our clients are continually surprised by the breadth of products and services provided by Plasmotec. A fundamental aspect of what we offer is our proven track record and expertise in caring for orphan tooling for a wide range of key market sectors. We have 30 years of experience in tool set up, operation and maintenance along with using the most up to date technology to bring out the best performance for each and every tool we run. Enjoy the following advantages by relocating your existing tooling: Increased output levels from machines running 24 hours a day and a range of machines to choose from, therefore avoiding delays. Utilising our on-site tool room and our comprehensive tool maintenance program.Improvements in consistency of product quality by having access to our optimisation and validation quality procedures.Cost effective tool upgrade options.Competitive unit prices for supply of your product.No set up fees. *No storage fees. * Talk to us about relocating your tooling. For further information and friendly advice contact us on 01280 701 335 or at sales@plasmotec.co.uk *Terms and conditions apply.
About Us
Plasmotec is a well established UK company based in Northamptonshire. We have been in the business of injection moulding and tool making since 1989 and pride ourselves in being able to offer our clients a comprehensive service for all of their plastic moulding needs.
The Plasmotec team comprises a broad range of skills and expertise across a variety of disciplines, all of which we believe are vital to the success of each and every project.

